Nauwkeuriger werken door automatisering
Industriële automatisering
Automatisering kun je inzetten om personeel uit te sparen, maar het kan ook gebruikt worden om er voor te zorgen dat de medewerker nauwkeuriger gaat werken en minder fouten maakt. Ook scheelt kosten en kan daar door zeer interessant zijn. Een mooi voorbeeld van dit laatste troffen we aan bij Polyplastic, een bedrijf dat onder andere kunststof vensters maakt voor caravans en campers.
B3 industrie biedt Polyplastic de helpende hand
Is de mens altijd een nauwkeurige werker? Dit is een vraag waar menig arbeidsdeskundige uren over kan uitweiden. De strekking van zijn verhaal zal dan zijn dat dit niet het geval is. Zeer veel oorzaken kunnen er voor zorgen dat de mens zeker niet altijd foutloos zal werken, ook al doet hij nog zo zijn best. Zeker bij routinehandelingen liggen er vele valkuilen in de weg met als gevolg dat een bepaald percentage van het werk niet goed uitgevoerd wordt. Dit is iets waar menig bedrijf rekening mee houdt en de kosten verrekent over de totale productie. Uiteraard is het zonde van alle moeite, de grondstoffen, de tijd en alle kosten die bij fouten niet leiden tot een positieve omzet. Op zeer veel manieren probeert men dan ook om de nauwkeurigheid van het personeel te verhogen. Bijvoorbeeld extra scholing, een goede werkomgeving, voldoende rust zijn een paar factoren die kunnen leiden tot minder productiefouten. Maar mensen blijven mensen. Het helemaal uitsluiten van fouten zal nooit voor 100% lukken. Bij het voorkomen van fouten kan automatisering een belangrijke rol spelen. Neem bijvoorbeeld de kassa van de supermarkt. Door gebruik te maken van de barcode op de verpakking van de producten hoeft men geen prijzen meer in te toetsen en zijn tikfouten niet meer mogelijk. De voordelen van automatisering vragen hier dan ook niet om nadere uitleg. Het spreekt voor zich dat een proces dat geheel automatisch uitgevoerd wordt natuurlijk geen last heeft van menselijke fouten (behalve dan in de programmatuur), maar lang niet elk proces is gemakkelijk geheel automatisch uit te voeren. Mensenhanden blijven dan ook noodzakelijk en dus moet gedeeltelijke automatisering de helpende hand bieden om het percentage fouten zo laag mogelijk te houden.
In de laatste fase
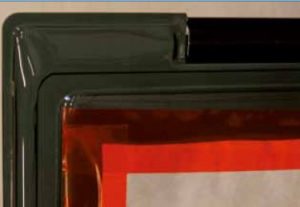
Zoals gezegd maakt Polyplastic kunststof vensters voor o.a. caravans. Ongeveer 60% van alle caravanvensters op de wereld komt van dit in Rotterdam gevestigde bedrijf. Dit zijn niet alleen zeer veel vensters, maar ook een zeer grote variëteit. Standaardisatie is namelijk bij caravans ver te zoeken omdat elk merk en elk type zijn eigen uitstraling wil hebben en met de vorm van de vensters kan dat zeer gemakkelijk. Om een dergelijk venster vanuit een vlakke plaat acrylaat te kunnen maken moeten er diverse stappen uitgevoerd worden, beginnend met het op maat zagen van het basismateriaal en het boren van diverse gaten. De plaat wordt in veel gevallen voorzien van een zeefdruk waarna men deze verhit en met een mal vormt tot de buitenschaal van het venster. Omdat veel vensters voor een betere isolatie dubbel uitgevoerd zijn moet er nog een tweede plaat in de buitenschaal gelijmd worden en moet de rand van het venster bijgefreesd worden voor het verkrijgen van het uiteindelijke venster. Als laatste stap moet op het venster een aluminium strip geperst worden die het draaiende deel van het vensterscharnier vormt. Het venster is daarvoor aan de bovenzijde voorzien van een verdiept gedeelte met daarin een groef voor de strip. Figuur 1 toont de linker bovenhoek van het venster. De aluminium strip is hier zwart en rechtsboven te zien. Ook de rechterkant van het venster ziet er nagenoeg hetzelfde uit en het is juist het feit dat de strip verdiept ligt dat tot problemen leidt bij de productie. De medewerker die namelijk de pers bedient, moet het venster exact positioneren. Doet hij dat niet, dan is de kans groot dat de pers ook de verhoogde delen van het venster raakt en daarmee al het voorafgaande werk vernielt. Ook is het van belang dat de aluminium strip exact horizontaal onder de pers gehouden wordt. Bij veel vensters is dit geen probleem, maar de caravanbranche gebruikt meer en meer gebogen vensters zoals het bovenvenster aan de voorkant van de caravan uit figuur 2. Ook hier moet het bedienend personeel goed opletten bij het instellen van de machine en het invoeren van het venster om niet met één druk op de knop het venster te vernielen. Bedenk hierbij dat een kunststof venster waarvan één van de hoekjes kapot geperst is niet meer bruikbaar is. Niet alleen is het dubbele venster lek, maar ook niet meer te repareren. Zelfs het allerkleinste scheurtje in het kunststof leidt tot volledige afkeuring van het venster dat, op het inpakken na klaar zou moeten zijn voor verzending naar de klant.
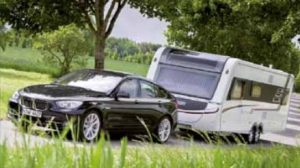
Flexibel
Just in time is ook bij het assembleren van caravans een eis die gesteld wordt aan de leveranciers van onderdelen. Voor Polyplastic betekent dit dat er over het algemeen gewerkt wordt met kleine orders van enkele tientallen vensters per uitvoering. De productie moet daarom ook zeer flexibel zijn als het gaat om het verwisselen van hulpmiddelen bij het productieproces. Alle machines zijn daarom zo uitgevoerd dat mallen zeer snel en gemakkelijk te verwisselen zijn en dat instellingen van zaag-, frees- en boormachines automatisch aangepast worden na het lezen van een barcode op de orderbon. Bij de persbank die ruim 10 jaar geleden geplaatst was kon men ook de nodige aanpassingen uitvoeren, maar producten veranderen met als gevolg dat er te veel en te vaak aangepast moest worden bij elke verandering in het productieproces. Daarnaast leverden met name de grote, sterk gekromde vensters veel problemen op. Meerdere medewerkers moesten er voor zorgen dat het venster op de juiste manier onder de pers gehouden werd. Hierbij werd veelal op de gok gewerkt met alle gevolgen van dien.
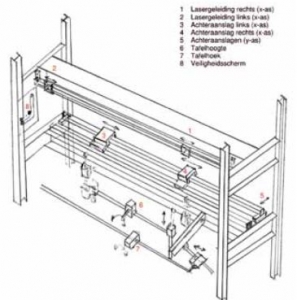
Met hulp van de computer
De nieuwe raamvormen leidden er uiteindelijk toe dat het percentage uitval na het persen van het scharnierdeel onacceptabel hoog geworden was en dat er of een grondige verbouwing van de bestaande machine of een nieuwe machine moest komen. Men koos voor het laatste. De heer John Coppers, hoofd van de technische afdeling en in zijn functie verantwoordelijk voor het totale machinepark van Polyplastic bedacht, onder het motto “je moet toch wat te doen hebben” zittend op de bank terwijl zijn vrouw TV aan het kijken was, het concept voor de nieuwe machine. Figuur 3 toont de schets die hij toen gemaakt heeft. Zoals te zien is, heeft de machine twee lasergeleiders die gebruikt worden om het venster exact te positioneren onder de pers. Twee aanslagen die links en rechts op de gewenste plaats gebracht worden en met een derde as naar voren of naar achteren bewogen kunnen worden, moeten er voor zorgen dat de pers op precies de gewenste plek op het aluminium drukt. Daarbij zorgt de instelling van de tafelhoogte en tafelhoek er voor dat het aluminium exact waterpas komt te liggen. In totaal zijn hier dan ook zeven servomotoren voor nodig die allemaal aangestuurd moeten worden vanuit een database met de parameters die horen bij het venster dat bewerkt wordt. De pers zelf bestaat uit 20 persblokken die hydraulisch bediend worden. Ook hier is het van belang dat het juiste aantal blokken gebruikt wordt en ook hier wordt de machine gestuurd vanuit de parameters in de database. In de tekening zijn overigens deze persblokken niet weergegeven. Nadat de heer Coppers zijn ideeën op papier had gezet, heeft hij Laurens Buying, directeur eigenaar van B3 industrie benaderd. B3 industrie is al sinds de oprichting 15 jaar geleden hofleverancier van Polyplastic met name om de projectmatige technische kennis binnen deze onderneming. Uitgaande van de handgetekende schets heeft Laurens het automatiseringsconcept bedacht dat in figuur 4 is weergegeven. Dit verhaal begint bij de CAD-software Alphacam die op de ontwikkelafdeling gebruikt wordt. Hieruit worden de parameters gehaald die nodig zijn voor de klembank. Deze worden in het SCADA-systeem van het klembank-systeem opgeslagen en zijn daar op te halen door de machine. Hiervoor dient de industriële PC die midden in de figuur is weergegeven. Op de PC is de barcodelezer aangesloten en via een industrieel netwerk wordt er gecommuniceerd met een PLC voor het sturen van de servomotoren en een touchscreen voor de bediening. Met een barcode-orderformulier kan de operator nu de juiste instellingen van de gehele klembank eenvoudig selecteren en volautomatisch en dus foutloos instellen. Niet in dit figuur opgenomen zijn de motordrives, de sturing voor de hydrauliek, alle sensoren en het veiligheidscircuit. Deze zijn allemaal aangesloten op de PLC en worden van daaruit bestuurd. De technische afdeling van Polyplastic is vervolgens aan het bouwen gegaan en tegelijkertijd heeft een geselecteerd team van mensen van diverse bedrijven – onder leiding van B3 industrie – gewerkt aan de applicatiesoftware, het engineeren en bouwen van de schakelkast met alle besturingseenheden.

Veiligheidsscherm
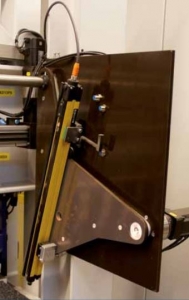
Het spreekt voor zich dat ook deze machine moet voldoen aan de machinerichtlijnen en dat er dus uitgebreide veiligheidsmaatregelen aanwezig moeten zijn. Zo is er een hek geplaatst zodat de achterkant van de machine niet zomaar bereikbaar is en gebruikt men een veiligheidslichtscherm om aan de voorkant te voorkomen dat iemand met zijn handen onder de pers terecht kan komen. Aangezien de machine voor zeer veel verschillende vensters ingezet wordt en elk venster een eigen dikte heeft, kon het lichtscherm niet vast gemonteerd worden. De heer Coppers bedacht voor het hoogteprobleem een fraaie oplossing. Zoals in figuur 5 te zien is, is het lichtscherm gemonteerd op een driehoekvormige plaat die met behulp van een servomotor gedraaid kan worden. Zo kan het lichtscherm volautomatisch op een dusdanige hoogte gesteld worden dat de onderste lichtbundel net over het venster heen schijnt. Dat bij het verdraaien deze lichtbundel iets naar voren of naar achteren bewogen wordt, is daarbij geen probleem.
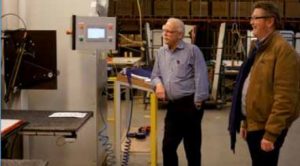
Het resultaat
Door de samenwerking van John Coppers en Laurens Buying (figuur 6) en de bedrijven die door B3 industrie als projectmatige partners ingeschakeld zijn, is er een zeer fraaie, flexibele machine ontstaan die maakt dat Polyplastic ook gemakkelijk nieuwe ontwikkelingen op het gebied van kunststof vensters aan kan. De caravanmarkt staat immers onder druk en er wordt dan ook hard gewerkt aan het ontwikkelen van nieuwe markten om het gat te vullen en te zorgen voor uitbreiding. Zo heeft men recent een UV-bestendige acrylaat plaat ontwikkeld die indrukwekkend slag- en krasvast is en die perfect lichtdoorlatend is. Een dergelijke plaat is voor zeer veel toepassingen te gebruiken. Te denken valt aan machineafschermingen (figuur 7), zonnepanelen, woningbouw, etc. Voor al deze applicaties kunnen kunststof vensters die met de nieuwe klembankmachine bewerkt zijn, prima ingezet worden.
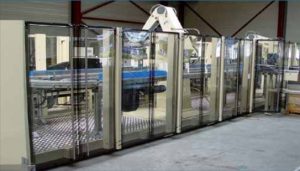